Metsä Fibre’s new bioproducts mill in Kemi is the largest single investment and the biggest project ever undertaken by the Finnish forest industry. The initial situation was not easy due to the increased space requirements caused by the corona pandemic, but the project was completed on schedule. This was facilitated by flexible space production and a local equipment rental company, as well as innovative solutions.
The factory’s smokestack on Taivaanranta is easily visible all the way to the E4 motorway. It is part of the new pulp mill in Kemi, which is part of Metsäfibre’s larger bioproduct mill project to process all production side streams. The large size of the project is reflected in the investment costs of more than €2 billion and the 70 hectares of the mill site.
This major project, which took around two and a half years to complete, was completed on time despite the tight schedule and despite the fact that the early phases of the project were characterised by the rapidly increasing need for workspace in the wake of the interest rate pandemic. Their delivery had to be brought forward as a result.
Aarre Pohjola, project manager for Metsä Fibre Oy’s site operations, says that the need for office space, for example, doubled.
– Fortunately, Ramirent Finland Oy was able to meet our needs, which enabled the project to be completed on schedule,” he says.
Requirement for new facilities
Requirement for new facilities
In total, nearly 900 worksite spaces were delivered to Metsä Fibre, making it one of Ramirent’s largest single deliveries of space elements. The customer required new or like-new facilities, covering a wide range of needs from social areas to offices, distribution kitchens, induction and corona testing facilities.
Due to the large size and requirements of the project, Ramirent had appointed its own project manager, Ismo Hyvönen, to be responsible for the delivery of the premises. He explains that the majority of the facilities were manufactured in Ramirent’s factory, and that in addition, sudden space requirements could be met with existing equipment.
– The fact that Metsä Fibre locked a deal with us well in advance of the start of the project and our own production facilities enabled us to prepare for such a large facility delivery without any scheduling problems, Hyvönen says.
Vesa Nurmi, Product Manager at Ramirent, also considers it important for the success of the project that regular follow-up meetings were held between the client and Ramirent throughout the project. Scheduling issues and the need for additions and changes were handled through good cooperation between Aarre Pohjola and Ismo Hyvönen, not forgetting the contribution of the foreman and installers on site.
“Cooperation was close and daily,” adds Aarre Pohjola.
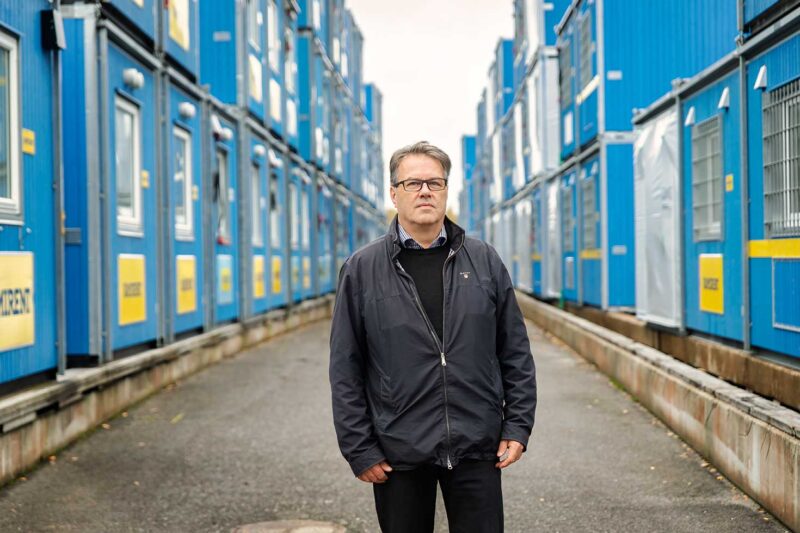
Ramirent’s equipment rental facility at Kemi plant
Ramirent’s Equipment Rental Facility at Kemi Plant
Ramirent also set up its own equipment rental facility at the Kemi bioproducts plant site, which included a main rental point and two satellite points located near the main gate of the plant.
– The coverage of the rental operation was an important advantage, as it allowed a quick and flexible response to the needs of the site. Ramirent supplied telehandlers, cranes, generators and other necessary equipment to the site, ensuring refuelling, service and maintenance,” says Aarre Pohjola.
Olli-Pekka Heikkilä, the foreman in charge at LTR-Rakennus Oy, also cites Ramirent’s proximity to the rental point as an absolute advantage. He was responsible for site services for LTR during the construction of the project.
– We were involved in the most intense phases of the project and were able to start the work on schedule because rental equipment such as heavy hand tools, shearers, floor sanders and heaters were quickly and easily available. We saved a significant amount of time and therefore costs by not having to travel long distances to get the equipment,” says Heikkilä.
Ramirent’s staff got to know each other during our one and a half year contract. The equipment was constantly needed, and cooperation was smooth and easy.
The mast climber hoist was delivered inside a high barrel
The mast climber hoist was delivered inside a high barrel
The project was supplied with a wide range of equipment for different phases of construction, from ground works to specialised industrial tools.
The responsible persons on the equipment rental side were Ramirent’s project manager Janne Aula, account managers Esa Simonen and Veikko Rantamaa, and Kalle Juntunen, the branch’s foreman. They say that this was the first time that the rental service was offered on such a large scale.
Demand was particularly high for telehandlers and lifts.
– At best, up to 20 telehandlersand more than 300 different types of lifts were in use at the same time. In some cases, there was not even time to return the equipment to the rental company; maintenance and statutory inspections had to be carried out on site,” they say.
The construction of the factory’s chimney was a particularly challenging phase, as the equipment had to fit inside the 105-metre-high chimney, which tapers upwards. The equipment supplied included telehandlers, hand washing sinks, heaters, forklifts and articulated boom lifts.
– We also ended up supplying a mast climber inside the barrel. It was a unique solution that allowed us to work at the desired height,” says Kalle Juntunen.
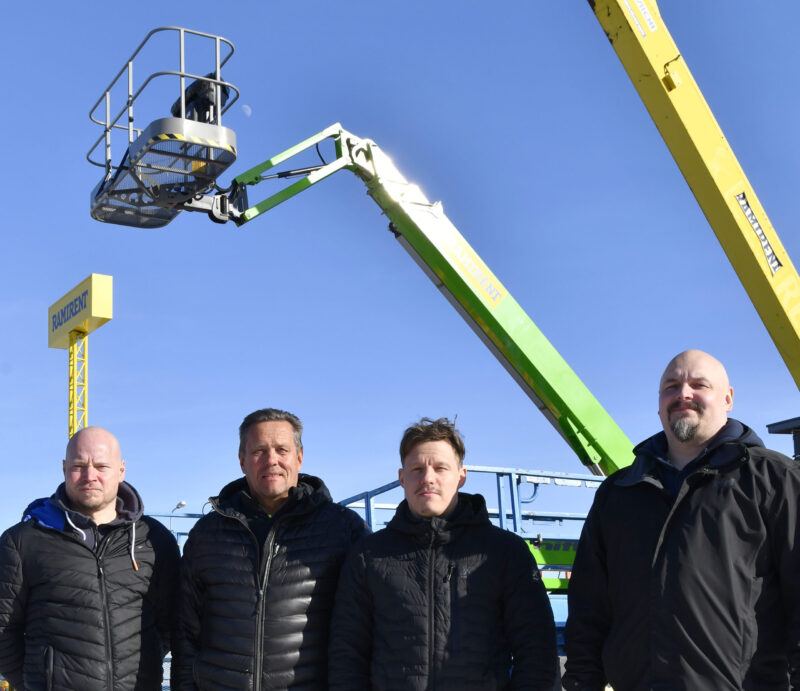